Is quality really free?
- Dr. Ulrich Harmes-Liedtke
- Jul 19, 2021
- 5 min read
Updated: 5 days ago
In the 1980s, the US-American quality guru, Philip B. Crosby, said, quality is free. [1,2] Crosby meant that the price not doing quality assurance is very high and always justifies the investment in quality.
One central goal of any quality management system is to reduce quality costs to the lowest practical level.
The figure shows that the cost of defects decreases as the quality of conformity increases towards perfection, during assessment and prevention increase. Theoretically, an “optimal” target quality was the sum of prevention, assessment, and error costs at a minimum. Efforts to increase quality above the optimum would increase total quality costs and would be inefficient. [3]
![Source: Juran’s Quality Control Handbook [3]](https://static.wixstatic.com/media/4da7f7_084bd11cafe0410296fb317e976b737e~mv2.png/v1/fill/w_902,h_640,al_c,q_90,enc_avif,quality_auto/4da7f7_084bd11cafe0410296fb317e976b737e~mv2.png)
In that sense, quality is a cost-benefit trade-off. On the one hand, there is the cost of good quality, which breaks down into appraisal and prevention costs. Appraisal costs are associated with measuring and monitoring activities related to quality. On the other hand, prevention costs are incurred to prevent or avoid quality problems. These costs are associated with the design, implementation, and maintenance of the quality management system.[4]
On the other hand, there are the costs of poor quality, which are divided into internal and external failure costs. Internal defect costs are incurred to correct defects before the goods reach the customer. These include waste, scrap, rework or rectification, and the cost of the internal product or service failure reasons. External error costs arise from customer feedback and complaints (repairs, reclamations, returns) and the associated administrative and communication costs.[4]
The metaphor of an iceberg is used to differentiate the costs of missing quality.[5] Thus, a minor part of quality costs such as complaints, rejection, rework, scrap or inspection and testing are easily visible. In contrast, the more significant part of quality costs is less visible. These include late delivery costs, inventory costs, premium shipping costs or loss of customer loyalty. The problem with these hidden costs is that they are difficult to quantify.
![Figure: Costs of Poor Quality [5]](https://static.wixstatic.com/media/4da7f7_4a3d84f7ad7742f2953491f8c5dfc85e~mv2.png/v1/fill/w_902,h_648,al_c,q_90,enc_avif,quality_auto/4da7f7_4a3d84f7ad7742f2953491f8c5dfc85e~mv2.png)
In principle, Crosby assumes that cost savings always justify investment in quality. Thus, if Crosby’s thesis were generally accurate, all companies would have to invest in quality management systems.
However, it is mainly large, internationally active corporations that certify and update their quality management systems regularly. In contrast, many SMEs have no formalised quality management in place. Moreover, in geographical terms, systems like ISO 9001 are less present in the Global South than in the North.
To better understand why many companies in the Global South do not use certified quality management systems, my Ecuadorian colleague, Mauro Rivadeneira (Corporación Q), and I conducted a non-representative survey with the support of ISO Tools. [6]
Between April and June 2021, 152 companies from twelve Latin American and Spain countries completed our questionnaire.
Country | Total | % |
Spain | 1 | 0,66% |
Paraguay | 1 | 0,66% |
Costa Rica | 2 | 1,32% |
Bolivia | 3 | 1,97% |
Panama | 4 | 2,63% |
Venezuela | 5 | 3,29% |
Chile | 7 | 4,61% |
Argentina | 13 | 8,55% |
Other Central American countries | 13 | 8,55% |
Peru | 14 | 9,21% |
Ecuador | 18 | 11,84% |
Colombia | 25 | 16,45% |
Mexico | 46 | 30,26% |
152 | 100,00% |
Source: Survey of Mesopartner and Corporación Q
More than half of the companies have been active for more than ten years. The remaining companies existed for 5 to 10 years (6.6%), 3 to 5 years (11.9%), 1 to 3 years 24.5%) and less than one year (4%). In terms of sectoral affiliation, the service sector (34.5%), manufacturing industry (24.7%) and the public sector (12.7%) dominated.
Operation time | Total | % |
1. less than one year | 6 | 3,97% |
2. between 1 and 3 years | 37 | 24,50% |
3. between 3 and 5 years | 18 | 11,92% |
4. between 5 and 10 | 10 | 6,62% |
5. more than ten years | 80 | 52,98% |
151 | 100,00% |
Source: Survey of Mesopartner and Corporación Q
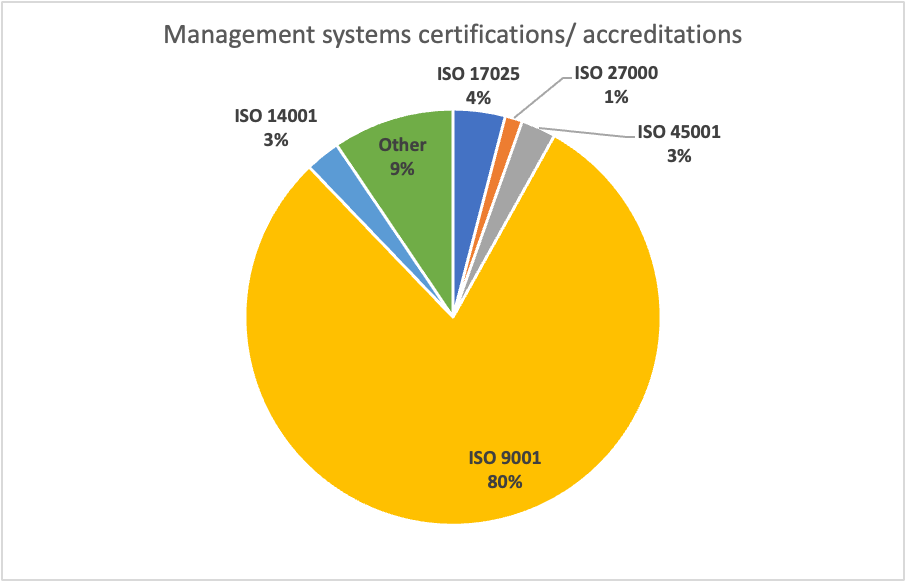
Only about 40% of the companies surveyed stated that they have or had a certified or accredited quality management system. Among the systems, ISO 9001 dominates, followed closely by ISO 14001 (environmental management), ISO 45001 (occupational safety) and accreditations of the ISO 17000 series for conformity assessment bodies.
The management systems of 30% of the companies have been in place for ten years or more. Another 30% have been certified for five to ten years and the rest of the certified companies for less than five years.
It raises concerns that 27% of the once certified companies have not renewed their management system certification. The reasons for this were manifold: the companies mentioned that customers did not demand certificates or that the cost of certification was too high. Other companies switched from the general ISO 9001 to more specific certification schemes.
We assumed that in companies without certification, the investment in quality exceeded the cost of tangible quality improvements. In the case of companies with certification, the result was the opposite.
In the case of the companies with certification, the costs of obtaining the certificate exceeded the adaptation of the production processes and personnel training. The companies without management system certification also invested in quality. Surprisingly, the non-certified companies also report high expenses for conformity assessment. These costs may be explained by the fact that these companies were previously certified or by a simple mistake in filling out the questionnaire. The transformation of production processes, staff training and consulting costs are also high. In both cases, costs for acquiring standards, payment for overtime or other representative costs were less relevant.
The costs of non-quality are similar in both groups. Overall, the costs of correcting defects, losses due to poor quality and the costs of complaints and warranty services dominate. The costs of inspection and other representative costs, on the other hand, were less critical.

Regarding the monetary costs of quality and non-quality, the survey did not generate any apparent results. In general, companies find it difficult to qualify the expenses of non-quality precisely. Therefore, we assume that the hidden costs of quality are generally underestimated. Overall, there is a need for further training among SMEs in Latin America and indeed in other world regions to assess the costs of quality.
On the other hand, it is noticeable that the offers of the certification bodies and quality consultants still seem expensive, especially for SMEs. In this respect, the certification bodies should make more effort to explain the benefits of their services and adapt the prices to the financial capacities of SMEs. At the same time, larger companies and the state are called upon to create incentives for investment in quality management systems by introducing quality requirements into procurement processes.
References
[1] Crosby, P. B. (1980). Quality is free: The art of making quality certain, Signet Book.
[2] Crosby, P. B. (1996). Quality is still free: making quality certain in uncertain times, McGraw-Hill Companies.
[3] Juran, J.M. and Gryna, F.M. (1988) Juran’s Quality Control Handbook. 4th Edition, McGraw-Hill, New York.
[4] ASQ, COST OF QUALITY (COQ); in: Quality Glossary Definition: Cost of quality, retrieved 16/07/21
[5] DeFeo, J. A. (2001). The tip of the iceberg, in: Quality progress 34(5): 29-37,
[6] ISO Tools (2020)., Costos de la No calidad Presentación de los resultados del estudio, Webinar
Comentários